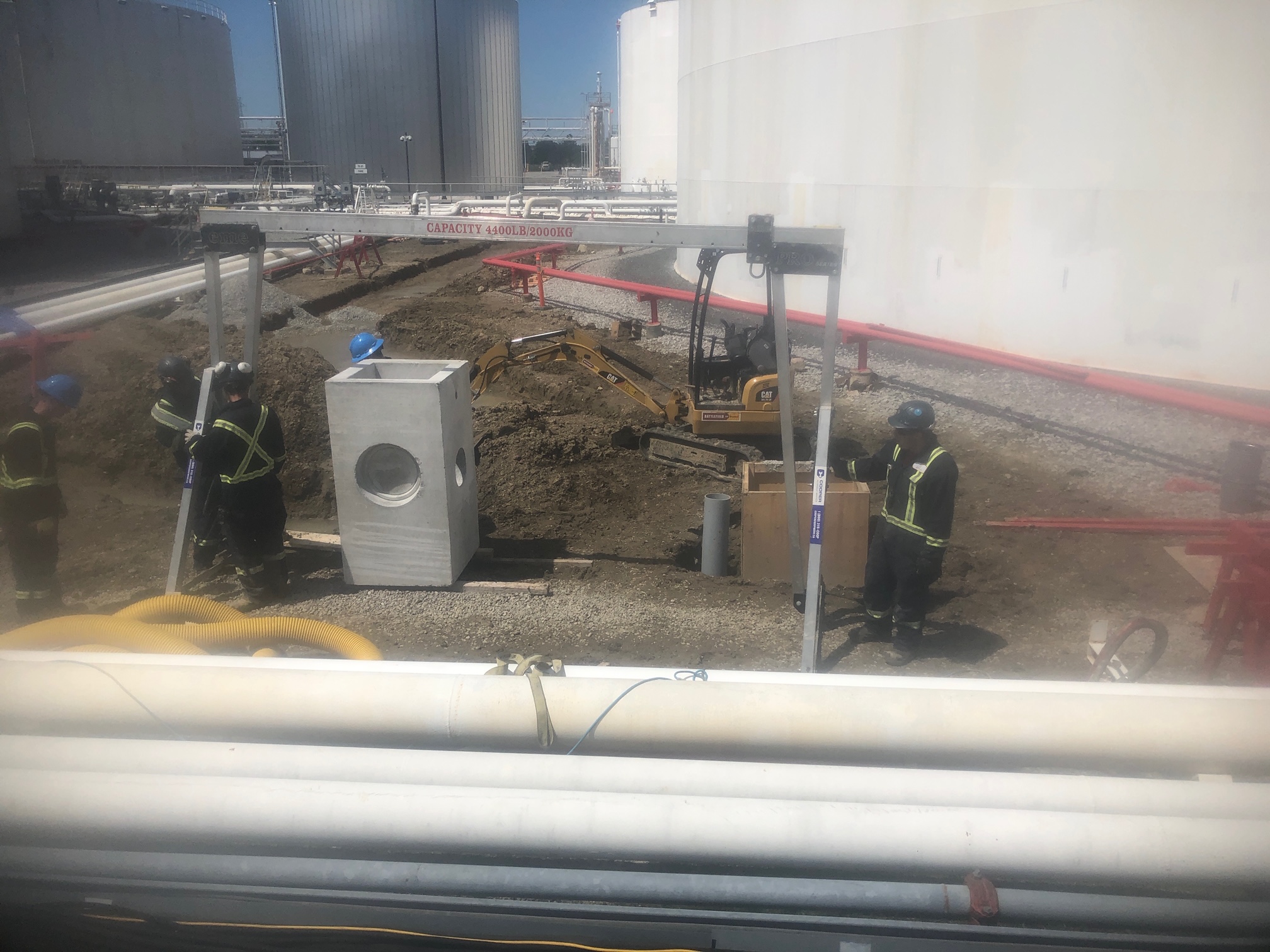
To maintain the world’s economy, petroleum—literally “rock oil”—remains vital. It is used in chemistry, plastics, heating, power generation, life-saving medicines, and the production of items such as contact lenses and heart valves. Its applications are diverse and ubiquitous. However, for most people, the term simply refers to the fuel that powers their vehicles and they rarely think about its other uses or its potential to cause serious harm to people, property, wildlife, and the environment if it is not responsibly stored.
At gas stations, airports, factories, and other industrial settings, petroleum is routinely stored in underground and above-ground storage tanks. Because it is inherently dangerous, it must be housed securely, with extensive measures in place to prevent spillage and to guarantee effective containment. It only needs one valve to develop a fault or one seal to perish to create a major incident involving financial loss and physical hazard. Moreover, regulatory bodies have the power to impose punitive fines on companies that are in breach of their safety obligations. This has costs in terms of not just money, but also reputation.
Environment Canada (EC) set out in its Storage Tank Systems Regulations more than 50 standards providing specifications for design and storage, leak detection devices, and spill containment equipment. Let’s look first at overfill protection.
Three Categories of Petroleum Overfill Prevention
Category 1 is the most basic form, relying almost entirely on manual operation. It requires the human agency to gauge the liquid levels in the tank and monitor all filling and transfer processes to ensure the valves are closed at the correct time. The data is not transmitted to a control room, and the readings are displayed locally without an alarm system.
Category 2 uses Automated Tank Gauging (ATG), it sends data to the control room, and has automated alarms but still needs manual intervention to control the safety valves.
Category 3 combines ATG and Overfill Prevention System (OPS) alarms using either a manual or automated switching system.
Automated Overfill Prevention Systems (AOPS)
In fully automated facilities, these systems are often installed in addition to ATG and OPS alarms. After a satisfactory risk analysis, AOPS is used to monitor fuel levels and regulate inflow under the guidance of sensors. In an emergency, the flow of oil will be shut down automatically and alerts will be sent to the monitoring personnel.
Spill Mitigation and Containment
Every system requires a failsafe, as even the most reliable, high-tech storage safety features can malfunction. The possibility may be remote, but the consequences could be devastating. For this reason, quick containment measures are needed. The most effective solution is to use frac tanks and portable containment berms. Frac tanks are commonly used in the petrochemical and fracking industries and are available in various sizes, with the largest being 21,000 gallons. This capacity should be more than adequate to provide temporary storage for a major over-spill until any faults in the main storage tank and OPS can be rectified and normality resumed.
Industry best practices for storage tanks now incorporate API 2350 prescriptive standards and IEC 61511 functional safety standards, which can increase costs. OPS not only ensures safety, but also helps to reduce those costs.