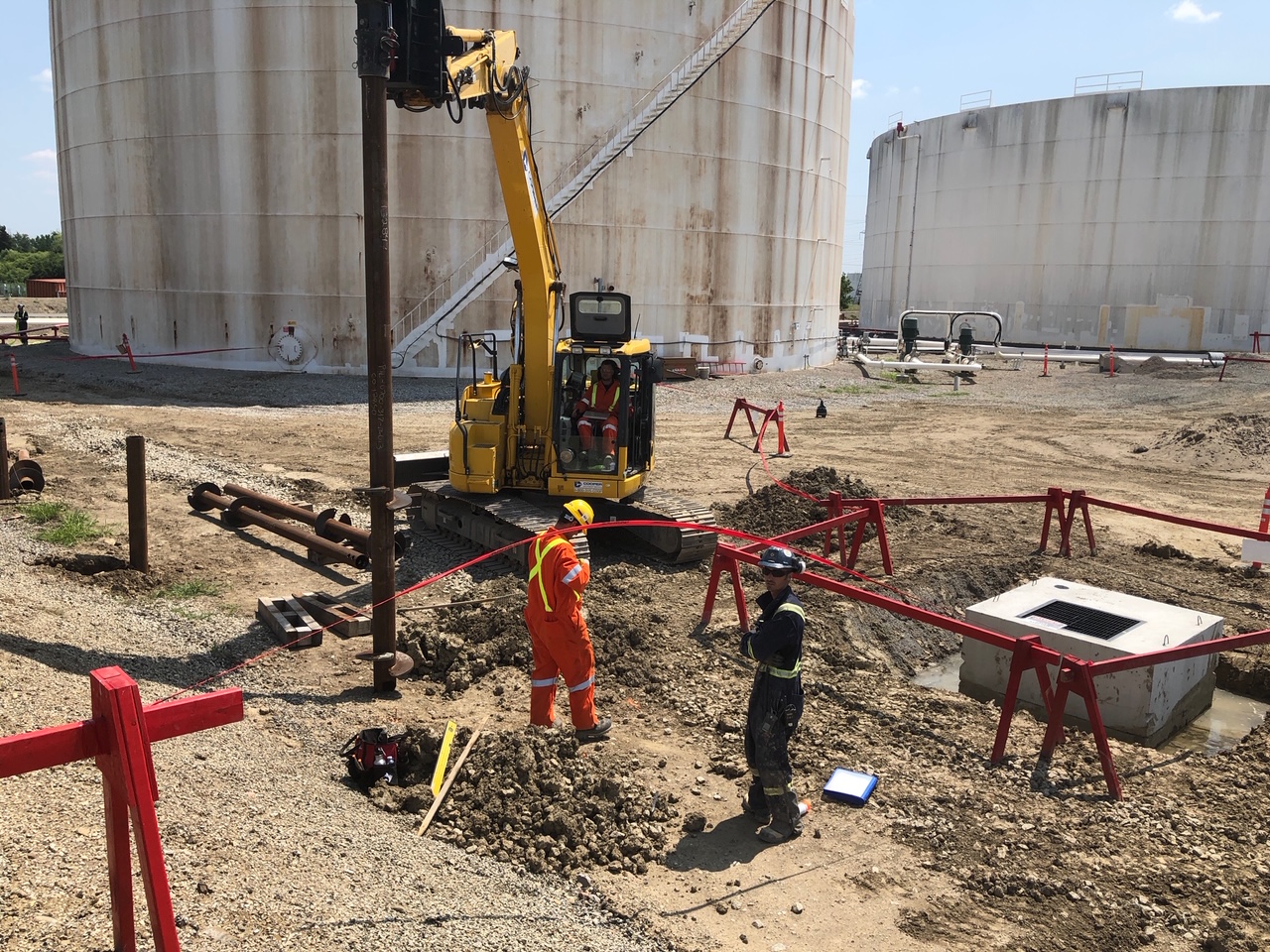
Maintaining and cleaning petroleum storage tanks is essential to prolong their life and reduce the risk of environmental contamination but planning and conducting maintenance activities can be a logistical challenge. Luckily, several new innovations are simplifying and expediting the process of cleaning and maintaining these tanks, keeping them working effectively for longer, improving worker safety and reducing the risk of leaks and spillages.
5 of the most exciting advancements are discussed in more detail below:
-
Automated monitoring
Manual inspections have previously required that tanks be drained and manual inspections performed, costing time and money. In contrast, automated monitoring systems use sensors to continuously monitor tank wall integrity, to check for corrosion and to report contamination or sediment buildup.
Using real-time data, problems can be identified early and plans made to resolve them before they result in a failure. By planning maintenance for a convenient opportunity, downtime is reduced, unnecessary cleaning is avoided, and safety is improved.
-
Robotic cleaning
The petroleum industry is very aware of the dangers of exposing workers to hazardous chemicals and fumes, so removing the need for manual entry is a huge step towards improving worker safety. Robotics is a field which looks set to deliver exceptional results, improving the quality of tank cleanliness while also safeguarding worker health.
Robots can be equipped with water jets and suction devices and use sensors to direct their attention to areas requiring cleaning or maintenance. They are remotely controlled, meaning that workers are not exposed to confined spaces, hazardous fumes or extreme heat but can still direct them to achieve the necessary result.
-
Bio-remediation
It is common for petroleum tanks to accumulate sludge but bio-remediation is an innovation which utilizes bacteria and microbes to break down and digest this sludge, converting it into water and carbon dioxide.
This cleaning method aligns well with Canada’s green energy strategy and can reduce both the cost of maintenance and its environmental impact.
-
Dry ice blasting
Dry ice blasting is the process through which compressed air is used to shoot pellets of dry ice at the interior surfaces of a petroleum storage tank, removing contaminants without leaving any harmful residues.
This cleaning method is non-abrasive and because it does not introduce any moisture into the tank, can protect against corrosion and extend the tank’s lifespan. It is a quick and cost-effective cleaning method that is rapidly gaining in popularity.
-
Mobile sludge treatment units
Mobile sludge treatment units can be very advantageous for businesses located in remote areas as they reduce the need to transport sludge extracted from petroleum tanks and reduce wastage.
They work by separating sludge into its component parts of water, oil and solids and recovering usable oil for the business’ benefit. By only removing contaminated water and the solids from site, disposal costs are reduced and the business can reduce its carbon footprint.
Conclusion
There are many scientific advancements which promise to revolutionise the petroleum industry, making tank maintenance and cleaning safer, more environmentally responsible and delivering cost efficiencies. These are some of the most promising solutions currently available to Canadian businesses.