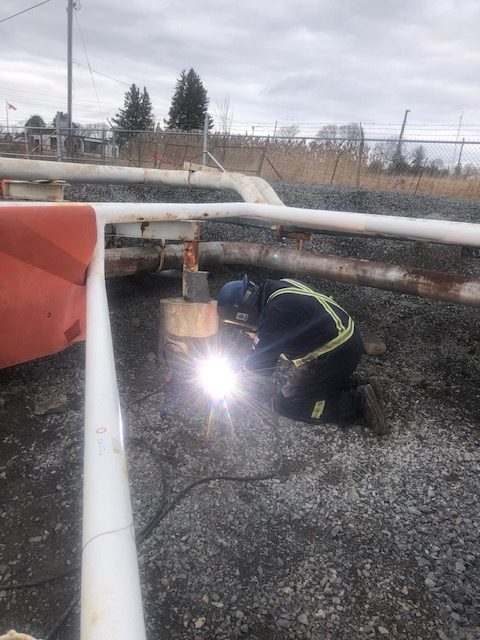
Custom welding can be the answer in many projects with tricky installations or issues, such as the installation of a new fuel tank. However, when you are considering your project and your bottom line, you may be tempted to have the welding done by someone without relevant experience on your staff to save money. After all, you could save some money, and how hard can it be?
Welding in general–and especially custom welding in fuel projects–requires real experience and comprehensive training. An inexperienced welder can create hazards, damage equipment and end up costing you more in time and money than you ever save by going this route. There are many mistakes a novice welder can make, including the three common ones below.
Being unable to control the heat
No matter what type of welding procedure is being done, the heat control and penetration have to be maintained and controlled at a steady pace. With thicker steel, for example, an experienced welder will add more weld beads to help ensure the piece being worked on is as secure as it possibly can be. Not being able to control the heat or penetration can have expensive consequences in terms of damage to the items being welded, and it can even result in harm to the welder and/or people nearby. This is especially true when the welder is working around petroleum or other fuels, which can pose their own hazards.
Not cleaning petroleum tanks or equipment properly
As an experienced welder will tell you, trying to weld on rusted, dirty or painted surfaces will not go well. These areas must be cleaned properly before the welder starts a weld bead; otherwise, the job will not turn out as well as it should. How it will be cleaned depends on the metal and the debris or coating in the way, but grinding is common. Without appropriate cleaning, the welds will be weaker because the dust, dirt, paint or rust takes heat away from the weld-metal surfaces.
Not following all safety protocols
A less experienced welder is likely going to come across equipment or tools they have never used before or haven’t used very often. Naturally, this will pose a safety issue to the person welding and potentially anyone else nearby. It’s very easy for someone to harm themselves using welding tools if they are not very familiar with them. In addition, a welder must be properly outfitted in the necessary protective clothing and gear to avoid harm from heavy sparks or ultralight.
If you need custom welding on your next petroleum project, you may think that your typical welder or someone else handy with tools on your team can handle the task. However, this can have a disastrous and expensive impact on your project and could cause harm to someone in your business. You could even end up in legal hot water due to safety regulations regarding the workplace and fuel projects in your area.
Don’t take any chances when it comes to your custom welding project on your fuel tank. Contact an experienced custom welding service provider for help today.